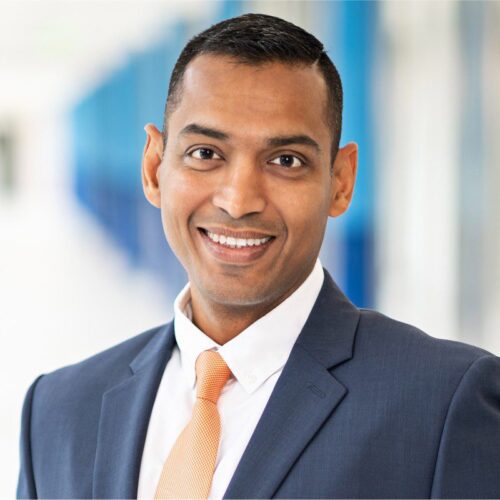
In Conversation: Trushar Agrawal, Senior Director and Head of Manufacturing at Kite Pharma
Kite, a Gilead Company, continues to grow its state-of-the-art cell therapy manufacturing facility in Frederick, Maryland. Since receiving FDA approval in April 2022, the site has expanded to more than 400 employees.
This past summer, Kite promoted biotech industry veteran Trushar Agrawal from his Director of QA role to Senior Director, Head of Manufacturing for the Frederick site. Agrawal will work to bring on new team members as the site ramps up commercial production of its CAR T-cell therapy product, which is used to treat people living with blood cancer.
We caught up with Agrawal to discuss his career, his leadership style and the site’s hiring approach and needs as it moves into an exciting future.
You were recently promoted to the Head of Manufacturing at Kite’s new Frederick facility after a 20-year career in the biopharma industry. What are some of the leadership lessons you’ve learned from your Pharma experiences and at Kite that you’re bringing to your new role?
One of the biggest things I’ve learned is: people are your biggest asset.
You can have a state-of-the-art facility and the most technologically advanced equipment, but you also need to take the time to nurture your talent and have a proactive strategy to engage and retain them. For me, an engaged team is everything. I’ve learned through experience that when you keep your talent engaged they’re happier, more productive and more likely to be invested in the mission long term.
I’ve also learned that you need to invest in training. Kite has a strong onboarding program for our new team members. On day one, they are set up with a peer mentor that supports them during the onboarding process. They also go through rigorous training for 6-8 months before starting to work on the manufacturing floor; as a result, they feel supported and ready for success.
How is your background in chemical engineering and as a Director of Quality an asset as you take on this leadership role?
When I first started my career, Quality was seen as a function just for regulatory compliance. Over time, I noticed that Pharma companies learned that Quality is also good business practice. Quality is a way of working, a mindset. Anytime I’m assessing a scenario or a challenge, my Quality background really helps me to evaluate risk, not just from the regulatory perspective, but what the impact could be on the patient.
My chemical engineering background helps me understand the technical nature of a problem.
I am very data-driven, and when I am making a decision with a good understanding of Quality regulations and the science, I have a better understanding of risk. I have always found that the combination of my engineering and Quality background has helped me successfully work through some challenging situations.
How would you characterize your leadership style?
I would describe it as servant leadership, and one that provides coaching and guidance.
Empowering people to make decisions that are appropriate for their role is very important. I feel that I should provide my team with resources and tools to make their own decisions because making decisions for them will not really help them.
I also find that as a leader I get the best from my team if I develop a personal relationship and build that trust first.
Is there a personality type or set of characteristics (soft skills, tech skills) that Kite looks for when searching for talent?
The number one thing for me: you must be patient-focused. Kite’s goal is to cure cancer, so we look for people who believe in our mission, and who understand that everything we do has a direct connection to the patient.
I also look for candidates who have a strong desire to strive for continuous improvement because in cell therapy, even though Kite already has commercial cell therapy products on the market, we are learning new things every day. Having a mindset of finding better ways of doing things is very important.
We look for team players that have a collaborative approach and an ability to work well with others. That’s also critical.
I think it’s also important for candidates to know that you don’t need a PhD or advanced degree to work at our site. We have a number of entry-level jobs that require high school or associate’s degrees. We also consider candidates that don’t have direct pharmaceutical experience. If you have the right mindset, some transferable skills, a desire to learn new things and the ability to thrive in a regulated environment, you can succeed in manufacturing at Kite.
What is the new hire experience like at the Frederick site and what opportunities exist for growth?
We strive to make a new hire’s experience great so when they get to work they have a good support system in place and a clear development plan so they know where they could go in their career with Kite.
We hire a lot of recent graduates, and many of them have different aspirations. It’s our job to understand their long-term career aspirations, and build a plan that keeps them engaged and helps them to reach their goals. That’s a win-win for both of us.
Creating cross functional training opportunities for our staff is also very important, especially when you are growing by leaps and bounds.
Kite is actively recruiting talent to join the Frederick team. What types of roles are in highest demand and what’s the best way for candidates to connect with Kite?
Yes, we are hiring for a variety of roles in quality control, cell manufacturing, engineering, training and maintenance at different levels of experience.
Interested candidates can check our careers page. We recently held an onsite recruitment event at our facility and shared more about the types of roles we are looking for.
What is your vision for the Frederick facility’s future?
About three years ago, the site was basically flatland and now we have an impressive state-of- the-art facility with about 275,000 square feet of finished space and 75,000 more square feet for expansion. The Frederick facility is the third commercial manufacturing facility in Kite’s global manufacturing network.
More patients and physicians are learning about our approved therapies so demand is growing. The Frederick site is pivotal for Kite’s operations, as it plays a key role in bringing our cell therapies to more patients that need them.
- About the Author
- Latest Posts
Steve brings nearly twenty years of experience in marketing and content creation to the WorkForce Genetics team. He loves writing engaging content and working with partners, companies, and individuals to share their unique stories and showcase their work. Steve holds a BA in English from Providence College and an MA in American Literature from Montclair State University. He lives in Frederick, Maryland with his wife, two sons, and the family dog.