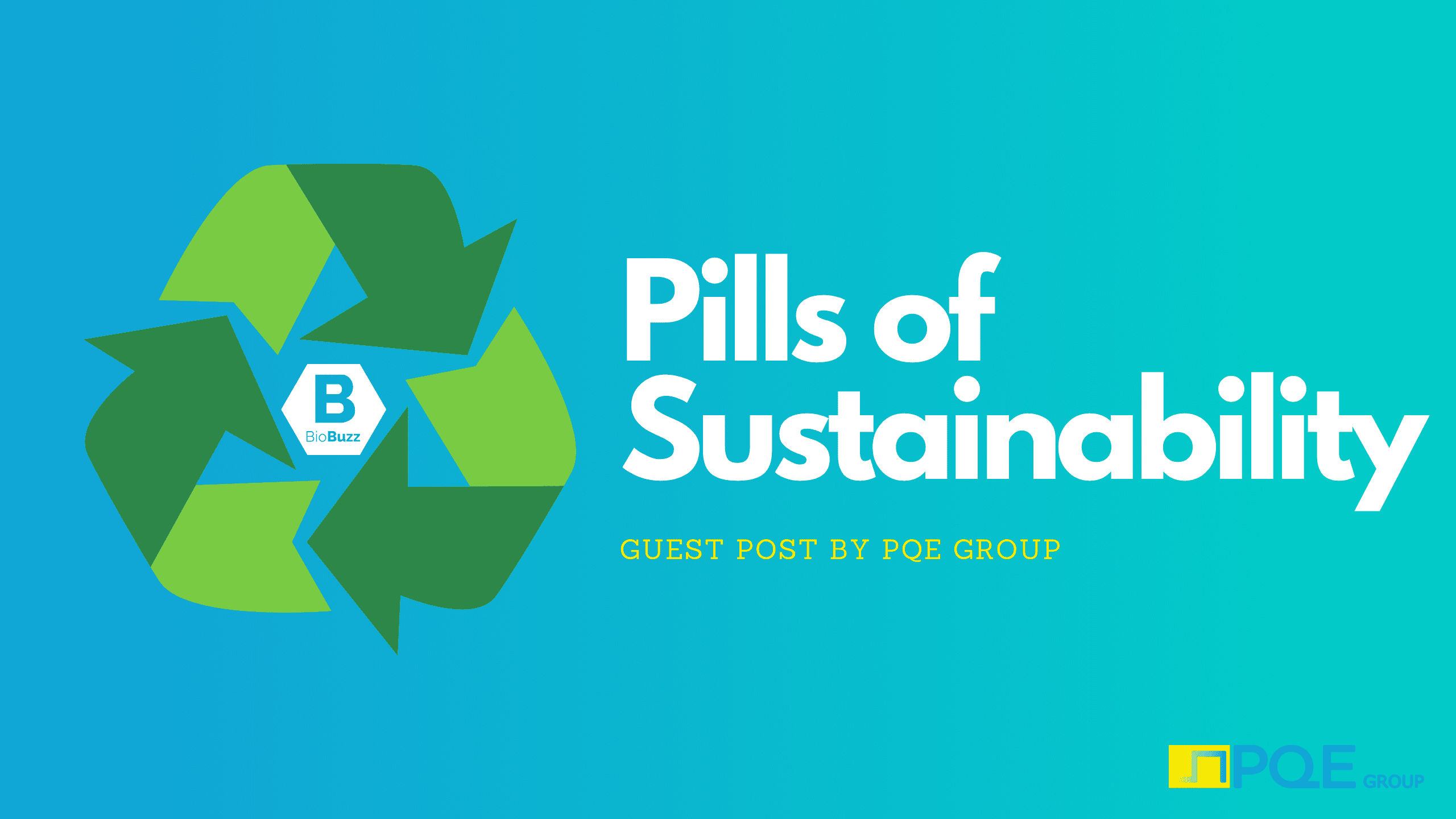
Pills of Sustainability
By Mariella Di Franco, Engineering Operations & Technical Director, PQE Group
PQE Group is a Corporate Partner who values community just as much as we do. Their expertise resides in pharma & API, MD & IVD and biotech. Enjoy the read and be sure to get in touch if you have an idea or perspective you’d like to share. BioBuzz welcomes guest posts and contributing writers with expertise on topics that are of interest. |
Healthcare rates are higher than the automotive sector in GHG emissions, urging companies to adopt policies to reduce their environmental impact. Sustainability is not a waste of money; in fact, it can reduce material and energy consumption, and increase shareholder value.
Let’s see some examples of implementing the “3 R’s” of sustainability (Reduce, Reuse, and Recycle) within the product design to increase efficiency and cut costs.
Pharma manufacturing has a high water use, with different qualities and temperatures utilized. In addition to reducing consumption and circulation by using efficient equipment and processes, there is a major interest in purifying wastewater and reusing it in the production cycle, rather than discharging significant volumes.
When Water for Injection (WFI) is mostly used at low temperatures, the possibility to generate WFI by membrane-based cold processes offers a great opportunity (thanks to Ph. Eur.’s WFI monograph change in 2017), yet one which few of the major players are willing to adopt.
Process modeling and computational fluid dynamics (CFD) simulation should be better employed for process development, control, and prediction, to optimize both the process and the sizing of the equipment/plant and to reduce energy and material consumption, arguably in every point of this article.
A notable application of CFD modeling is in HVAC systems, a major energy consumer in Pharma. The results allow us to eliminate contamination/stagnancy and avoid system over-design, consequently reducing costs and energy.
In addition to quality and process control, process analytical technology (PAT) is fundamental for digitalization and sustainability practice. Digital twin is a combination of monitoring, analysis, and simulation. By analyzing data and testing various scenarios, bottlenecks/areas of improvement are identified, supporting right-first-time manufacturing and reducing costs, energy, and waste.
Flow chemistry enables us to reduce dimensions, materials, energy, and waste while handling hazardous materials safely. Micro-reactors are highly practical in changing from batch to continuous with remarkable advantages: very efficient mixing and heat transfer, higher productivity, yield and selectivity, safe and controlled execution of reactions, straightforward scale-up, low hold-up, and reagent use. Micro-reactors are a valuable option to consider for homogenous reactions.
- About the Author
- Latest Posts
BioBuzz is a community led, experience focused, biotech and life sciences media and events company. BioBuzz highlights regional breaking news, industry professionals, jobs, events, and resources for business and career growth. Their weekly newsletter is subscribed to by thousands in the BioHealth Capital Region and Greater Philadelphia as the go-to for industry updates.